Łączenie dwóch kompresorów to proces, który może znacząco zwiększyć wydajność systemu pneumatycznego. Warto jednak zrozumieć, jakie są podstawowe zasady oraz techniki, które należy zastosować, aby osiągnąć zamierzony efekt. Przede wszystkim, przed przystąpieniem do łączenia kompresorów, należy upewnić się, że oba urządzenia mają podobne parametry techniczne. Oznacza to, że ich ciśnienie robocze oraz wydajność powinny być zbliżone. W przeciwnym razie jeden z kompresorów może pracować na niekorzyść drugiego, co prowadzi do nieefektywności i potencjalnych uszkodzeń. Kolejnym krokiem jest wybór odpowiedniego sposobu połączenia. Można zastosować różne metody, takie jak połączenie równoległe lub szeregowe. Połączenie równoległe pozwala na zwiększenie wydajności, natomiast połączenie szeregowe może być stosowane w sytuacjach wymagających wyższego ciśnienia.
Jakie są zalety łączenia dwóch kompresorów w systemach pneumatycznych
Łączenie dwóch kompresorów niesie ze sobą wiele korzyści, które mogą znacznie poprawić funkcjonowanie systemu pneumatycznego. Przede wszystkim zwiększa to ogólną wydajność systemu, co jest kluczowe w przypadku większych zakładów przemysłowych lub warsztatów. Dzięki połączeniu dwóch kompresorów można uzyskać większą ilość sprężonego powietrza w krótszym czasie, co przekłada się na szybsze wykonywanie prac oraz lepszą jakość produkcji. Kolejną zaletą jest możliwość redundancji. W przypadku awarii jednego z kompresorów drugi może przejąć jego funkcje, co minimalizuje ryzyko przestojów i strat finansowych związanych z brakiem dostępu do sprężonego powietrza. Dodatkowo łączenie kompresorów pozwala na optymalizację kosztów eksploatacyjnych. W dłuższej perspektywie czasowej może to prowadzić do oszczędności związanych z energią oraz konserwacją sprzętu.
Jakie są najczęstsze błędy przy łączeniu dwóch kompresorów
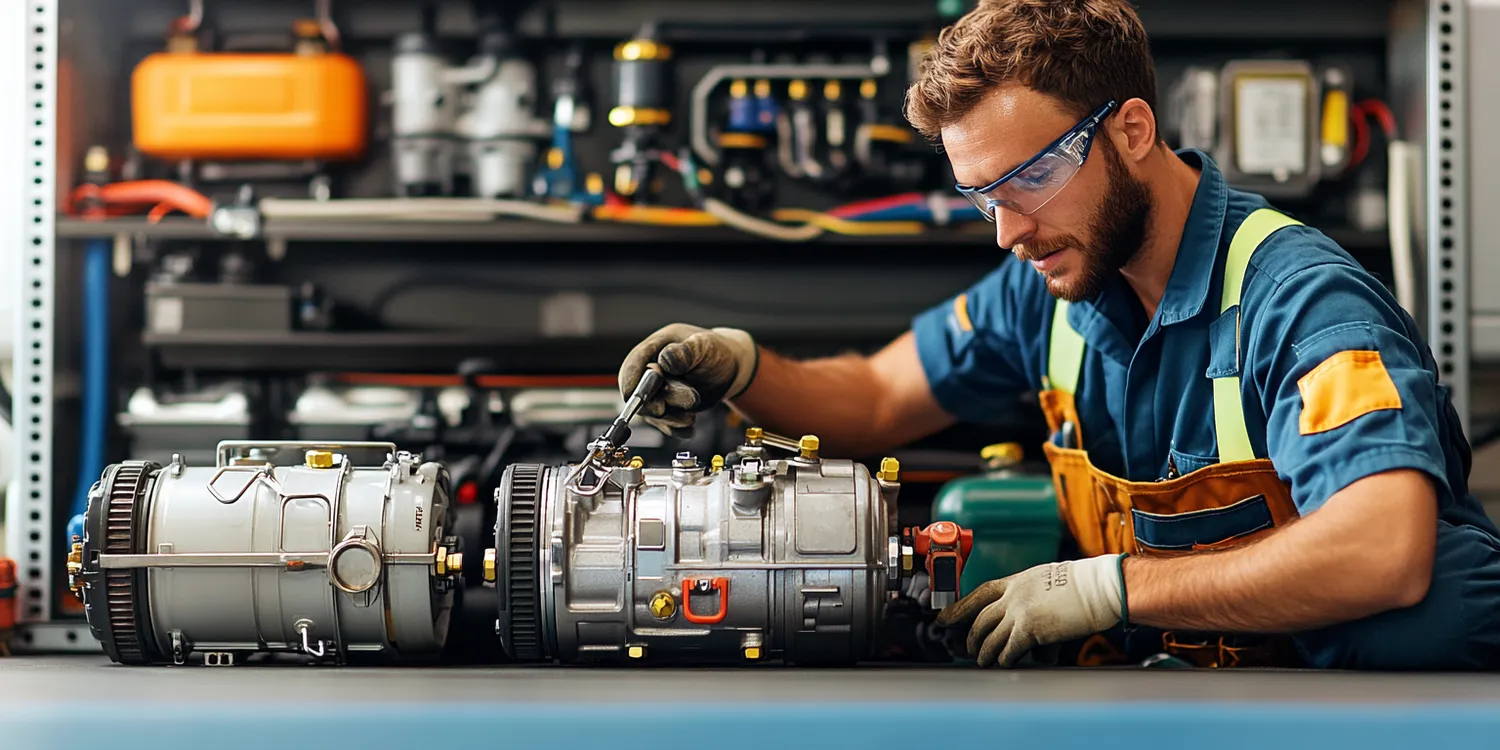
Podczas łączenia dwóch kompresorów istnieje wiele pułapek, które mogą prowadzić do problemów w działaniu całego systemu. Jednym z najczęstszych błędów jest niewłaściwe dobranie parametrów technicznych obu urządzeń. Niezgodność ciśnienia roboczego lub wydajności może skutkować nieefektywną pracą lub nawet uszkodzeniem jednego z kompresorów. Innym istotnym błędem jest zaniedbanie kwestii instalacji rur i zaworów. Niewłaściwie dobrane elementy mogą prowadzić do spadków ciśnienia lub wycieków sprężonego powietrza, co negatywnie wpływa na efektywność całego systemu. Również brak odpowiedniej konserwacji obu urządzeń przed ich połączeniem może prowadzić do szybszego zużycia komponentów oraz awarii. Nie można zapominać o regularnym monitorowaniu pracy kompresorów po ich połączeniu. Ignorowanie sygnałów ostrzegawczych lub brak reakcji na zmiany w wydajności mogą prowadzić do poważnych problemów w przyszłości.
Jakie narzędzia i materiały są potrzebne do połączenia kompresorów
Aby skutecznie połączyć dwa kompresory, niezbędne jest przygotowanie odpowiednich narzędzi oraz materiałów. Przede wszystkim warto zaopatrzyć się w zestaw kluczy, który umożliwi montaż i demontaż elementów instalacji. Kluczowe będą również wkrętaki, które pozwolą na precyzyjne dokręcenie śrub oraz złączeń. W przypadku instalacji rur niezbędne mogą być także piły do metalu lub specjalistyczne narzędzia do cięcia tworzyw sztucznych, jeśli zastosowane będą rury PVC. Warto również mieć pod ręką uszczelki, które zapewnią szczelność połączeń oraz zapobiegną wyciekom sprężonego powietrza. Dodatkowo, przydatne mogą okazać się manometry, które pozwolą na monitorowanie ciśnienia w systemie oraz zawory zwrotne, które zabezpieczą przed cofaniem się powietrza. Nie można zapominać o odpowiednich materiałach do mocowania, takich jak opaski zaciskowe czy taśmy uszczelniające.
Jakie są kluczowe kroki w procesie łączenia kompresorów
Łączenie dwóch kompresorów wymaga staranności oraz przestrzegania określonych kroków, aby zapewnić prawidłowe działanie całego systemu. Pierwszym krokiem jest dokładne zaplanowanie układu instalacji, co obejmuje wybór miejsca dla obu kompresorów oraz trasę dla rur. Ważne jest, aby miejsce było dobrze wentylowane i dostępne dla serwisu. Następnie należy przygotować oba urządzenia do montażu, co może obejmować odłączenie ich od zasilania oraz sprawdzenie stanu technicznego. Kolejnym krokiem jest zamontowanie rur i zaworów zgodnie z wcześniej opracowanym planem. Należy zwrócić szczególną uwagę na to, aby wszystkie połączenia były szczelne i dobrze dokręcone. Po zakończeniu montażu warto przeprowadzić testy ciśnieniowe, aby upewnić się, że nie ma wycieków powietrza. Jeśli wszystko działa poprawnie, można przystąpić do uruchomienia systemu.
Jakie są różnice między połączeniem równoległym a szeregowym kompresorów
Połączenie dwóch kompresorów może odbywać się na dwa główne sposoby: równolegle lub szeregowo, a wybór odpowiedniej metody ma kluczowe znaczenie dla efektywności systemu pneumatycznego. Połączenie równoległe polega na tym, że oba kompresory pracują jednocześnie, co pozwala na zwiększenie wydajności sprężonego powietrza. Taki układ jest idealny w sytuacjach, gdy potrzebna jest duża ilość powietrza w krótkim czasie. Dzięki temu można osiągnąć lepszą stabilność ciśnienia oraz zmniejszyć obciążenie każdego z urządzeń, co przekłada się na ich dłuższą żywotność. Z kolei połączenie szeregowe polega na tym, że jeden kompresor zasila drugi, co skutkuje uzyskaniem wyższego ciśnienia roboczego. Taka konfiguracja może być korzystna w sytuacjach wymagających dużych wartości ciśnienia, jednak wiąże się z ryzykiem przeciążenia jednego z urządzeń oraz ewentualnymi problemami z wydajnością.
Jakie są zalecenia dotyczące konserwacji połączonych kompresorów
Konserwacja połączonych kompresorów jest kluczowa dla zapewnienia ich długotrwałego i efektywnego działania. Regularne przeglądy techniczne powinny obejmować kontrolę stanu filtrów powietrza oraz oleju, ponieważ ich zanieczyszczenie może prowadzić do obniżenia wydajności urządzeń. Ważne jest również monitorowanie poziomu oleju w silnikach kompresorów oraz jego regularna wymiana zgodnie z zaleceniami producenta. Należy także zwrócić uwagę na stan uszczelek i zaworów – ich zużycie może prowadzić do wycieków sprężonego powietrza i obniżenia efektywności całego systemu. Dodatkowo warto przeprowadzać regularne testy ciśnieniowe oraz kontrolować manometry w celu wykrywania ewentualnych nieprawidłowości w działaniu urządzeń. Utrzymanie czystości wokół kompresorów również ma znaczenie – kurz i brud mogą wpływać na ich pracę oraz prowadzić do szybszego zużycia komponentów.
Jakie są koszty związane z łączeniem dwóch kompresorów
Koszty związane z łączeniem dwóch kompresorów mogą się znacznie różnić w zależności od wielu czynników, takich jak rodzaj używanego sprzętu czy skomplikowanie instalacji. Przede wszystkim należy uwzględnić koszty zakupu dodatkowych elementów instalacyjnych, takich jak rury, zawory czy manometry. W przypadku bardziej zaawansowanych systemów pneumatycznych konieczne mogą być także inwestycje w automatyczne sterowanie lub monitoring pracy urządzeń. Koszt robocizny to kolejny istotny aspekt – jeśli prace montażowe będą wykonywane przez specjalistyczną firmę, należy doliczyć wynagrodzenie dla fachowców. Warto również pamiętać o przyszłych kosztach eksploatacyjnych związanych z konserwacją i serwisowaniem połączonych kompresorów.
Jakie są najczęstsze pytania dotyczące łączenia dwóch kompresorów
Wiele osób zastanawia się nad różnymi aspektami związanymi z łączeniem dwóch kompresorów i często pojawiają się pytania dotyczące tego procesu. Jednym z najczęściej zadawanych pytań jest to, czy można łączyć różne modele kompresorów. Odpowiedź brzmi: tak, ale należy upewnić się, że mają one podobne parametry techniczne oraz ciśnienie robocze. Innym popularnym pytaniem jest to, jakie są korzyści płynące z takiego rozwiązania – głównie chodzi o zwiększoną wydajność i możliwość redundancji w przypadku awarii jednego z urządzeń. Osoby planujące montaż często pytają także o to, jakie narzędzia będą potrzebne do wykonania tej operacji – klucze, wkrętaki oraz materiały uszczelniające to podstawowy zestaw niezbędny do pracy. Często pojawia się też pytanie o konserwację połączonych kompresorów – regularne przeglądy techniczne oraz monitorowanie stanu filtrów powietrza to kluczowe elementy utrzymania sprzętu w dobrej kondycji.
Jakie są najlepsze praktyki przy łączeniu kompresorów w systemach przemysłowych
Łączenie kompresorów w systemach przemysłowych wymaga zastosowania najlepszych praktyk, aby zapewnić ich efektywność oraz niezawodność. Przede wszystkim, kluczowe jest przeprowadzenie dokładnej analizy potrzeb zakładu przed podjęciem decyzji o połączeniu urządzeń. Należy określić, jakie ciśnienie i wydajność są wymagane do realizacji procesów produkcyjnych. Warto również zainwestować w nowoczesne technologie, takie jak systemy monitorowania pracy kompresorów, które pozwalają na bieżąco śledzić ich wydajność oraz wykrywać ewentualne problemy. Dobrze zaplanowana instalacja rur i zaworów ma ogromne znaczenie dla prawidłowego funkcjonowania systemu – należy unikać ostrych zakrętów oraz zbyt długich odcinków, które mogą powodować straty ciśnienia. Regularne szkolenie personelu odpowiedzialnego za obsługę kompresorów również przyczynia się do zwiększenia efektywności i bezpieczeństwa pracy.