Destylator przemysłowy to urządzenie, które służy do separacji cieczy na podstawie różnicy w temperaturze wrzenia. Proces ten jest kluczowy w wielu branżach, takich jak chemiczna, petrochemiczna czy spożywcza. W destylacji wykorzystuje się zasadę, że różne substancje mają różne temperatury wrzenia. W praktyce oznacza to, że po podgrzaniu mieszaniny cieczy, substancja o najniższej temperaturze wrzenia przechodzi w stan gazowy jako pierwsza, a następnie jest skraplana i zbierana w osobnym naczyniu. Destylatory przemysłowe są wykorzystywane do produkcji alkoholu, oczyszczania wody, a także w procesach chemicznych do uzyskiwania czystych substancji chemicznych. W zależności od potrzeb, destylatory mogą mieć różne rozmiary i konstrukcje, od małych jednostek laboratoryjnych po ogromne instalacje przemysłowe.
Rodzaje destylatorów przemysłowych i ich charakterystyka
W przemyśle istnieje wiele różnych typów destylatorów, które są dostosowane do specyficznych potrzeb produkcyjnych. Najpopularniejsze z nich to destylatory prostokątne, kolumnowe oraz frakcyjne. Destylatory prostokątne są najprostsze w budowie i często stosowane w mniejszych zakładach produkcyjnych. Działają na zasadzie jednorazowego podgrzewania cieczy i skraplania pary. Z kolei destylatory kolumnowe są bardziej zaawansowane technologicznie i pozwalają na wielokrotne oddzielanie substancji w jednym procesie. Dzięki zastosowaniu kolumny z wypełnieniem lub talerzami, możliwe jest uzyskanie wyższej czystości produktów końcowych. Destylatory frakcyjne natomiast umożliwiają separację wielu składników jednocześnie, co jest szczególnie przydatne w przemyśle petrochemicznym.
Jakie są kluczowe komponenty destylatora przemysłowego
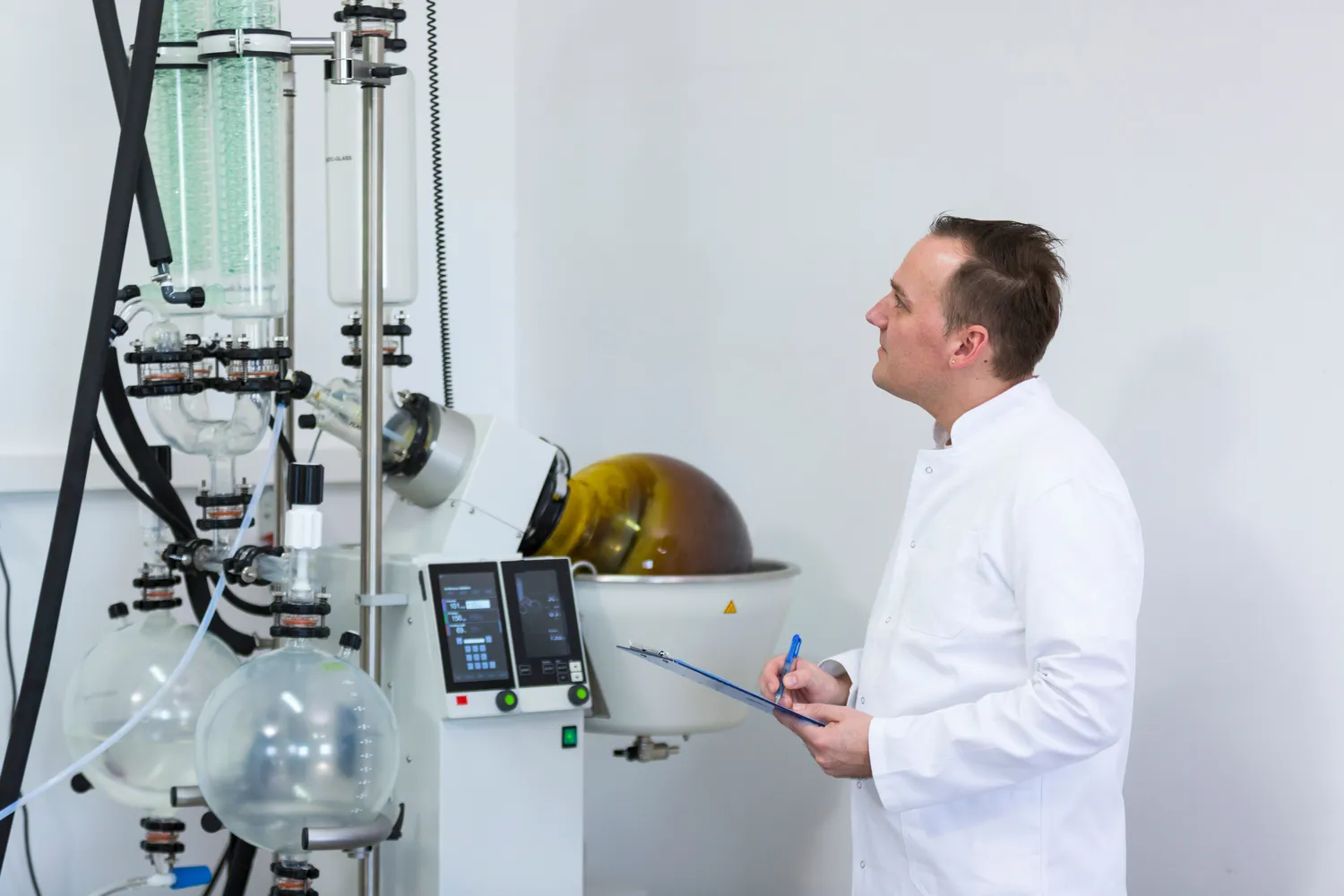
Każdy destylator przemysłowy składa się z kilku kluczowych komponentów, które współpracują ze sobą w celu efektywnego przeprowadzenia procesu destylacji. Podstawowym elementem jest zbiornik na ciecz, który jest podgrzewany do odpowiedniej temperatury. W przypadku destylatorów kolumnowych istotną rolę odgrywa również kolumna destylacyjna, która zawiera talerze lub wypełnienie umożliwiające wielokrotne kondensowanie pary. Kolejnym ważnym elementem jest skraplacz, który chłodzi parę i przekształca ją z powrotem w ciecz. Oprócz tych podstawowych komponentów, destylatory często wyposażone są w systemy kontroli temperatury oraz ciśnienia, co pozwala na precyzyjne zarządzanie procesem. Dodatkowo mogą być stosowane różne urządzenia pomocnicze, takie jak pompy czy filtry, które wspierają cały proces produkcji.
Jakie są korzyści z używania destylatorów przemysłowych
Użycie destylatorów przemysłowych przynosi wiele korzyści zarówno dla producentów, jak i dla konsumentów. Przede wszystkim pozwalają one na uzyskanie wysokiej czystości produktów chemicznych oraz innych substancji płynnych. Dzięki temu możliwe jest spełnienie rygorystycznych norm jakościowych wymaganych przez różne branże. Ponadto proces destylacji jest bardzo efektywny energetycznie, co przekłada się na niższe koszty produkcji oraz mniejsze zużycie surowców. Destylatory mogą być również dostosowane do różnych rodzajów surowców oraz wymagań produkcyjnych, co czyni je niezwykle wszechstronnymi narzędziami w przemyśle. Co więcej, nowoczesne technologie stosowane w budowie destylatorów umożliwiają automatyzację procesów oraz ich zdalne monitorowanie, co zwiększa bezpieczeństwo pracy oraz redukuje ryzyko awarii.
Jakie są najczęstsze problemy z destylatorami przemysłowymi
Podczas eksploatacji destylatorów przemysłowych mogą wystąpić różne problemy, które wpływają na efektywność procesu oraz jakość uzyskiwanych produktów. Jednym z najczęstszych problemów jest zatykanie kolumny destylacyjnej, co może prowadzić do obniżenia wydajności oraz jakości destylacji. Zatykanie może być spowodowane osadzaniem się zanieczyszczeń lub nieodpowiednim doborem parametrów procesowych. Innym istotnym problemem jest niewłaściwe zarządzanie temperaturą, które może prowadzić do niepełnej separacji substancji oraz powstawania niepożądanych produktów ubocznych. W przypadku destylatorów frakcyjnych, niewłaściwe ustawienie talerzy lub wypełnienia może skutkować niską efektywnością separacji. Dodatkowo, awarie systemów chłodzenia mogą prowadzić do przegrzewania pary i uszkodzenia sprzętu. Regularne przeglądy techniczne oraz odpowiednie szkolenie personelu są kluczowe dla minimalizacji ryzyka wystąpienia tych problemów.
Jakie są koszty związane z zakupem destylatora przemysłowego
Koszty zakupu destylatora przemysłowego mogą się znacznie różnić w zależności od wielu czynników, takich jak typ urządzenia, jego rozmiar oraz zastosowane technologie. Proste destylatory prostokątne mogą kosztować od kilku tysięcy do kilkunastu tysięcy złotych, podczas gdy bardziej zaawansowane destylatory kolumnowe czy frakcyjne mogą wymagać inwestycji rzędu setek tysięcy złotych. Oprócz samego zakupu, należy również uwzględnić koszty instalacji oraz uruchomienia urządzenia, które mogą być znaczące, zwłaszcza w przypadku dużych instalacji przemysłowych. Dodatkowo, warto brać pod uwagę koszty eksploatacyjne, takie jak zużycie energii, konserwacja oraz ewentualne naprawy. W dłuższej perspektywie czasowej, dobrze dobrany destylator może przynieść znaczne oszczędności dzięki zwiększonej efektywności produkcji oraz lepszej jakości produktów.
Jakie są innowacje technologiczne w dziedzinie destylacji przemysłowej
W ostatnich latach w dziedzinie destylacji przemysłowej nastąpił znaczny postęp technologiczny, który przyczynił się do zwiększenia efektywności i bezpieczeństwa procesów produkcyjnych. Jednym z najważniejszych trendów jest automatyzacja procesów destylacyjnych, która pozwala na precyzyjne zarządzanie parametrami pracy urządzeń. Dzięki zastosowaniu nowoczesnych systemów monitorowania i kontroli możliwe jest zdalne sterowanie procesami oraz szybkie reagowanie na zmiany w warunkach pracy. Innowacyjne technologie pozwalają także na zastosowanie bardziej zaawansowanych materiałów konstrukcyjnych, które zwiększają odporność urządzeń na korozję i wysokie temperatury. Kolejnym interesującym rozwiązaniem są systemy odzysku ciepła, które pozwalają na zmniejszenie zużycia energii poprzez wykorzystanie ciepła odpadowego generowanego podczas procesu destylacji.
Jakie są wymagania prawne dotyczące użytkowania destylatorów przemysłowych
Użytkowanie destylatorów przemysłowych wiąże się z koniecznością przestrzegania szeregu wymogów prawnych i regulacyjnych, które mają na celu zapewnienie bezpieczeństwa pracy oraz ochrony środowiska. Przed rozpoczęciem działalności związanej z destylacją konieczne jest uzyskanie odpowiednich zezwoleń oraz spełnienie norm dotyczących emisji zanieczyszczeń do atmosfery i wód gruntowych. W wielu krajach istnieją szczegółowe przepisy dotyczące budowy i eksploatacji urządzeń przemysłowych, które muszą być przestrzegane przez właścicieli zakładów produkcyjnych. Dodatkowo, pracownicy obsługujący destylatory muszą przejść odpowiednie szkolenia dotyczące bezpieczeństwa pracy oraz obsługi urządzeń. Regularne audyty i kontrole techniczne są również istotnym elementem zapewnienia zgodności z obowiązującymi przepisami.
Jakie są przyszłe kierunki rozwoju technologii destylacyjnej
Przyszłość technologii destylacyjnej zapowiada się obiecująco dzięki ciągłemu rozwojowi innowacyjnych rozwiązań oraz rosnącemu zainteresowaniu ekologicznymi metodami produkcji. W miarę jak świat staje się coraz bardziej świadomy problemów związanych ze zmianami klimatycznymi i ograniczeniem zasobów naturalnych, branża przemysłowa poszukuje sposobów na zwiększenie efektywności energetycznej procesów produkcyjnych. Można spodziewać się dalszego rozwoju technologii odzysku ciepła oraz zastosowania odnawialnych źródeł energii w procesach destylacyjnych. Również rozwój sztucznej inteligencji i analizy danych ma potencjał do rewolucjonizacji sposobu zarządzania procesami produkcyjnymi poprzez optymalizację parametrów pracy urządzeń w czasie rzeczywistym. Ponadto rosnące zainteresowanie biotechnologią może prowadzić do opracowania nowych metod separacji substancji chemicznych opartych na naturalnych procesach biologicznych.
Jakie są najlepsze praktyki dotyczące konserwacji destylatorów przemysłowych
Aby zapewnić długotrwałe i efektywne działanie destylatorów przemysłowych, niezwykle istotna jest regularna konserwacja urządzeń. Kluczowym elementem jest przeprowadzanie systematycznych przeglądów technicznych, które pozwalają na wykrycie ewentualnych usterek zanim staną się poważnym problemem. Ważne jest również czyszczenie kolumny destylacyjnej oraz innych komponentów urządzenia z nagromadzonych osadów czy zanieczyszczeń, co pozwala na utrzymanie wysokiej wydajności procesu separacji substancji. Oprócz tego warto stosować odpowiednie smary i środki ochrony przed korozją dla elementów narażonych na działanie wysokich temperatur i agresywnych substancji chemicznych. Szkolenie personelu obsługującego urządzenia jest równie istotne – pracownicy powinni być świadomi zasad bezpiecznej obsługi oraz procedur konserwacyjnych.
Jakie są różnice między destylatorami przemysłowymi a laboratoryjnymi
Destylatory przemysłowe i laboratoryjne różnią się przede wszystkim skalą produkcji oraz zastosowaniem. Destylatory przemysłowe są zaprojektowane do pracy w dużych instalacjach, gdzie wymagane jest przetwarzanie znacznych ilości cieczy, natomiast destylatory laboratoryjne są mniejsze i służą głównie do badań oraz eksperymentów. W przemyśle kluczowe jest uzyskanie wysokiej wydajności oraz ciągłości procesu, co często wiąże się z bardziej skomplikowanymi systemami automatyzacji. Z kolei w laboratoriach istotna jest precyzja i możliwość przeprowadzania różnych eksperymentów w kontrolowanych warunkach. Różnice te wpływają również na konstrukcję urządzeń, gdzie destylatory przemysłowe często mają bardziej zaawansowane systemy chłodzenia i kontroli temperatury, podczas gdy laboratoria mogą korzystać z prostszych rozwiązań.