Destylacja rozpuszczalników to proces, który polega na oddzieleniu składników mieszaniny na podstawie różnicy ich temperatur wrzenia. W praktyce oznacza to, że podczas podgrzewania cieczy, składniki o niższej temperaturze wrzenia parują jako pierwsze, a następnie są skraplane i zbierane w osobnym naczyniu. Kluczowym elementem tego procesu jest zastosowanie odpowiedniego sprzętu, takiego jak kolumna destylacyjna, która umożliwia wielokrotne skraplanie i parowanie, co zwiększa czystość uzyskiwanego produktu. Ważne jest również, aby kontrolować temperaturę oraz ciśnienie w systemie, ponieważ te czynniki mają bezpośredni wpływ na efektywność destylacji. W przypadku rozpuszczalników organicznych, takich jak etanol czy aceton, proces ten może być stosunkowo prosty, jednak w przypadku bardziej złożonych mieszanin konieczne może być zastosowanie dodatkowych technik, takich jak frakcjonacja.
Jakie są różnice między destylacją a innymi metodami separacji
W kontekście separacji składników mieszanin chemicznych istnieje wiele metod, które różnią się od destylacji. Jedną z najpopularniejszych alternatyw jest ekstrakcja, która polega na wykorzystaniu rozpuszczalnika do wydobycia określonych substancji z materiału stałego lub innej cieczy. Ekstrakcja może być bardziej efektywna w przypadku substancji o podobnych temperaturach wrzenia, gdzie destylacja mogłaby nie być wystarczająco skuteczna. Inną metodą jest filtracja, która polega na oddzieleniu ciał stałych od cieczy za pomocą porowatego materiału. W przeciwieństwie do destylacji, filtracja nie opiera się na różnicy temperatur wrzenia, co czyni ją mniej uniwersalną w przypadku mieszanin ciekłych. Ponadto istnieją techniki takie jak chromatografia, które pozwalają na separację składników na podstawie ich interakcji z fazą stacjonarną i ruchomą.
Jakie są zastosowania destylacji rozpuszczalników w przemyśle
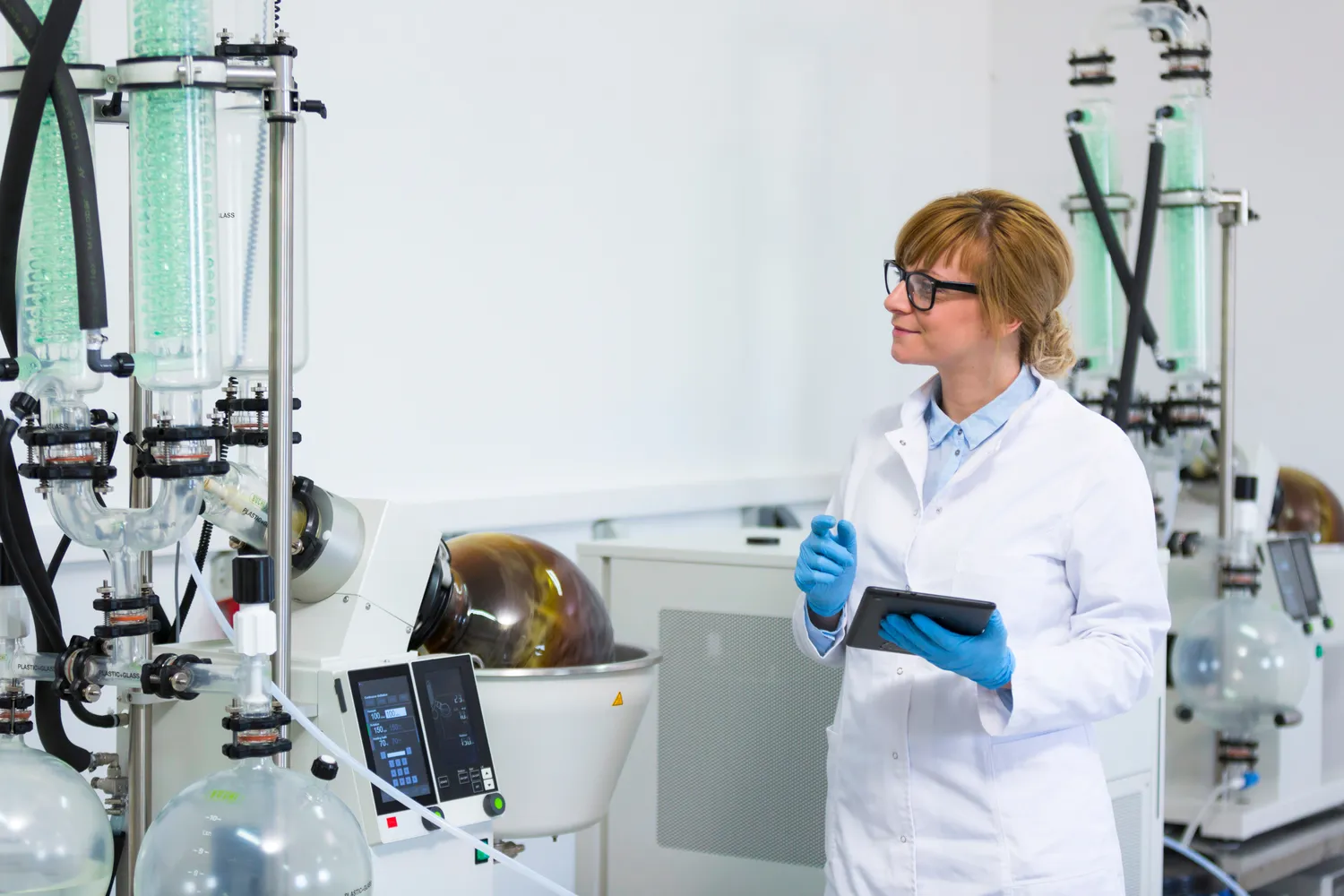
Destylacja rozpuszczalników znajduje szerokie zastosowanie w różnych gałęziach przemysłu. W przemyśle chemicznym jest kluczowym procesem wykorzystywanym do oczyszczania surowców oraz produktów końcowych. Na przykład w produkcji alkoholu etylowego destylacja pozwala na uzyskanie wysokiej czystości trunków poprzez usunięcie niepożądanych substancji i zanieczyszczeń. W branży farmaceutycznej proces ten jest niezbędny do produkcji leków o wysokiej jakości, gdzie czystość substancji czynnych ma kluczowe znaczenie dla skuteczności terapeutycznej. Ponadto destylacja jest wykorzystywana w przemyśle petrochemicznym do separacji różnych frakcji ropy naftowej, co pozwala na uzyskanie paliw oraz innych produktów chemicznych. W laboratoriach naukowych destylacja służy do przygotowywania prób do badań oraz analizy chemicznej.
Jakie są najczęstsze problemy podczas procesu destylacji
Podczas przeprowadzania destylacji rozpuszczalników mogą wystąpić różne problemy, które mogą wpłynąć na efektywność procesu oraz jakość uzyskiwanego produktu. Jednym z najczęstszych problemów jest nieodpowiednia kontrola temperatury, co może prowadzić do niepełnej separacji składników lub ich degradacji. Zbyt wysoka temperatura może spowodować przegrzanie cieczy i powstawanie niepożądanych produktów ubocznych. Innym wyzwaniem jest obecność zanieczyszczeń w surowcach wejściowych, które mogą wpływać na wyniki destylacji i obniżać jakość końcowego produktu. Warto również zwrócić uwagę na kondensatory, które muszą być odpowiednio chłodzone, aby skutecznie skraplać pary. Problemy mogą także wynikać z niewłaściwego ustawienia kolumny destylacyjnej lub użycia niewłaściwych materiałów eksploatacyjnych.
Jakie są różne rodzaje destylacji stosowane w przemyśle
W przemyśle chemicznym oraz farmaceutycznym można spotkać różne rodzaje destylacji, które są dostosowane do specyficznych potrzeb i właściwości separowanych substancji. Najpopularniejszym rodzajem jest destylacja prosta, która polega na jednorazowym podgrzewaniu cieczy i zbieraniu skroplonej pary. Jest to technika stosunkowo łatwa do przeprowadzenia, jednak ma swoje ograniczenia, zwłaszcza w przypadku mieszanin o zbliżonych temperaturach wrzenia. W takich sytuacjach bardziej efektywna może być destylacja frakcyjna, która wykorzystuje kolumnę destylacyjną do wielokrotnego skraplania i parowania. Dzięki temu możliwe jest uzyskanie wyższej czystości składników. Innym rodzajem jest destylacja azeotropowa, która ma zastosowanie w przypadku mieszanin tworzących azeotropy, czyli mieszaniny o stałym składzie, które nie zmieniają się podczas destylacji. W takich przypadkach konieczne może być dodanie innego rozpuszczalnika, aby zmienić właściwości azeotropu i umożliwić skuteczną separację. Oprócz tych metod istnieje także destylacja próżniowa, która polega na obniżeniu ciśnienia w systemie, co pozwala na destylację substancji w niższych temperaturach.
Jakie są kluczowe czynniki wpływające na efektywność destylacji
Efektywność procesu destylacji rozpuszczalników zależy od wielu czynników, które należy starannie kontrolować, aby uzyskać pożądane rezultaty. Jednym z najważniejszych elementów jest temperatura wrzenia poszczególnych składników mieszanki. Różnice te powinny być wystarczająco duże, aby umożliwić skuteczną separację podczas podgrzewania. Kolejnym istotnym czynnikiem jest ciśnienie panujące w systemie; obniżenie ciśnienia może znacznie zwiększyć efektywność procesu, szczególnie w przypadku substancji o wysokich temperaturach wrzenia. Ważne jest również odpowiednie dobranie sprzętu, takiego jak kolumna destylacyjna czy kondensator, które muszą być dostosowane do specyfiki separowanej mieszaniny. Dodatkowo czas trwania procesu oraz prędkość podgrzewania mają znaczenie dla jakości uzyskiwanego produktu; zbyt szybkie podgrzewanie może prowadzić do niepełnej separacji lub powstawania niepożądanych produktów ubocznych.
Jakie są nowoczesne technologie wspomagające proces destylacji
W ostatnich latach rozwój technologii przyczynił się do znacznej poprawy efektywności procesów destylacyjnych. Nowoczesne urządzenia wyposażone są w zaawansowane systemy monitorowania i kontroli parametrów procesu, co pozwala na precyzyjne dostosowanie warunków pracy do specyfiki danej mieszaniny. Przykładem innowacyjnych rozwiązań są kolumny destylacyjne z zastosowaniem nanotechnologii, które umożliwiają lepsze wykorzystanie powierzchni kontaktu między fazami ciekłą a gazową. Dzięki temu możliwe jest osiągnięcie wyższej efektywności separacji przy mniejszych stratach energii. Warto również wspomnieć o automatyzacji procesów destylacyjnych; nowoczesne systemy sterowania pozwalają na zdalne monitorowanie i zarządzanie procesem w czasie rzeczywistym, co zwiększa bezpieczeństwo oraz redukuje ryzyko błędów ludzkich. Dodatkowo rozwijane są technologie związane z odzyskiem ciepła, które pozwalają na zmniejszenie kosztów operacyjnych poprzez ponowne wykorzystanie energii cieplnej generowanej podczas procesu.
Jakie są zagrożenia związane z procesem destylacji
Podczas przeprowadzania procesu destylacji rozpuszczalników istnieje wiele zagrożeń, które mogą wpłynąć na bezpieczeństwo pracowników oraz jakość uzyskiwanego produktu. Jednym z głównych ryzyk jest możliwość wystąpienia pożaru lub eksplozji spowodowanej obecnością łatwopalnych substancji chemicznych oraz wysokimi temperaturami stosowanymi w procesie. Dlatego niezwykle ważne jest przestrzeganie zasad BHP oraz stosowanie odpowiednich środków ochrony osobistej przez pracowników obsługujących urządzenia destylacyjne. Innym zagrożeniem są toksyczne opary wydobywające się podczas podgrzewania niektórych substancji; dlatego konieczne jest zapewnienie odpowiedniej wentylacji oraz stosowanie filtrów ochronnych. Dodatkowo niewłaściwe ustawienie sprzętu lub błędy w monitorowaniu parametrów procesu mogą prowadzić do nieefektywnej separacji składników lub ich degradacji, co z kolei wpływa na jakość końcowego produktu.
Jakie są przyszłe kierunki rozwoju technologii destylacji
Przyszłość technologii destylacji rozpuszczalników zapowiada się obiecująco dzięki ciągłemu postępowi naukowemu oraz technologicznemu. W miarę jak rośnie zapotrzebowanie na czystsze i bardziej efektywne metody separacji substancji chemicznych, badacze poszukują nowych materiałów oraz technologii, które mogłyby poprawić wydajność procesów destylacyjnych. Jednym z obiecujących kierunków rozwoju jest zastosowanie nanomateriałów w konstrukcji kolumn destylacyjnych; materiały te mogą zwiększyć powierzchnię kontaktu między fazami oraz poprawić wymianę ciepła. Ponadto rozwijane są technologie związane z integracją procesów chemicznych i fizycznych; przykładem może być połączenie destylacji z innymi metodami separacyjnymi, takimi jak ekstrakcja czy adsorpcja, co pozwala na uzyskanie jeszcze wyższej czystości produktów końcowych. Warto również zwrócić uwagę na rozwój systemów automatyzacji i sztucznej inteligencji w procesach przemysłowych; inteligentne algorytmy mogą optymalizować parametry pracy urządzeń w czasie rzeczywistym, co przekłada się na większą efektywność energetyczną oraz redukcję kosztów operacyjnych.
Jakie są najważniejsze aspekty ekologiczne związane z procesem destylacji
W kontekście rosnącej świadomości ekologicznej oraz potrzeby minimalizacji wpływu przemysłu na środowisko naturalne, aspekty ekologiczne związane z procesem destylacji stają się coraz bardziej istotne. Proces ten często wiąże się z dużym zużyciem energii cieplnej oraz emisją substancji lotnych do atmosfery; dlatego ważne jest poszukiwanie rozwiązań mających na celu ograniczenie tych negatywnych skutków. Jednym z podejść jest wdrażanie technologii odzysku ciepła, które pozwalają na ponowne wykorzystanie energii generowanej podczas procesu destylacyjnego do podgrzewania innych mediów lub do ogrzewania budynków przemysłowych. Ponadto istotnym aspektem jest zarządzanie odpadami powstającymi podczas procesu; odpady te powinny być odpowiednio segregowane i przetwarzane zgodnie z obowiązującymi normami ekologicznymi.