Budowa maszyn pneumatycznych to temat, który zyskuje na znaczeniu w różnych branżach przemysłowych. Maszyny te wykorzystują energię sprężonego powietrza do wykonywania różnorodnych zadań, co czyni je niezwykle wszechstronnymi i efektywnymi. W procesie budowy takich maszyn kluczowe jest zrozumienie podstawowych elementów, które składają się na ich konstrukcję. Do najważniejszych komponentów należą cylindry pneumatyczne, zawory, sprężarki oraz różnego rodzaju przewody i złączki. Każdy z tych elementów pełni istotną rolę w funkcjonowaniu maszyny, a ich odpowiedni dobór i montaż mają ogromny wpływ na wydajność całego systemu. Cylindry pneumatyczne są odpowiedzialne za przekształcanie energii sprężonego powietrza w ruch mechaniczny, co pozwala na realizację wielu zadań, takich jak podnoszenie, przesuwanie czy formowanie materiałów. Zawory kontrolują przepływ powietrza w systemie, a sprężarki dostarczają niezbędną energię do działania maszyn.
Jakie są główne zastosowania maszyn pneumatycznych w przemyśle
Maszyny pneumatyczne znajdują szerokie zastosowanie w różnych dziedzinach przemysłu, co czyni je niezwykle ważnym narzędziem w nowoczesnej produkcji. Ich wszechstronność sprawia, że można je wykorzystać w takich branżach jak motoryzacja, elektronika, budownictwo czy przemysł spożywczy. W przemyśle motoryzacyjnym maszyny pneumatyczne są często wykorzystywane do montażu komponentów oraz do testowania jakości produktów. Dzięki swojej precyzji i szybkości działania umożliwiają one efektywne wykonywanie skomplikowanych operacji. W branży elektronicznej maszyny te służą do automatyzacji procesów montażowych oraz pakowania produktów. W budownictwie natomiast znajdują zastosowanie w narzędziach takich jak młoty udarowe czy wiertnice pneumatyczne, które ułatwiają prace związane z obróbką materiałów budowlanych. Przemysł spożywczy również korzysta z rozwiązań pneumatycznych, zwłaszcza w zakresie pakowania i transportu produktów.
Jakie są zalety i wady budowy maszyn pneumatycznych
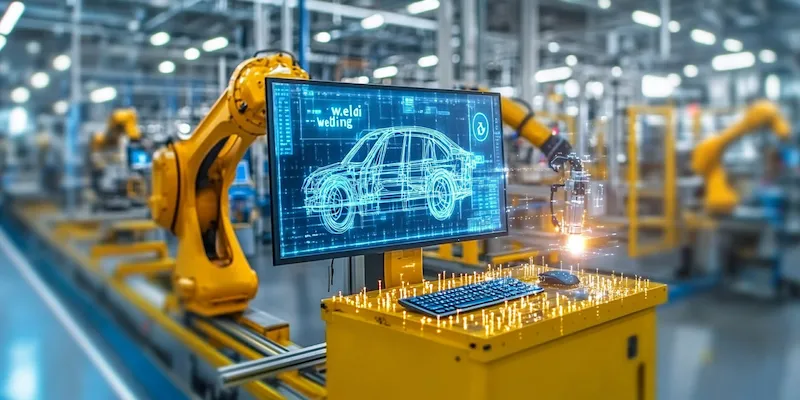
Budowa maszyn pneumatycznych wiąże się z wieloma zaletami, ale także pewnymi wadami, które warto rozważyć przed podjęciem decyzji o ich wdrożeniu. Jedną z największych zalet systemów pneumatycznych jest ich prostota oraz łatwość w obsłudze. Maszyny te charakteryzują się niską wagą oraz kompaktowymi rozmiarami, co ułatwia ich instalację i transport. Dodatkowo działają one cicho i nie emitują szkodliwych substancji chemicznych, co czyni je bardziej ekologicznymi niż inne systemy napędowe. Kolejną istotną zaletą jest możliwość precyzyjnego sterowania siłą i prędkością działania maszyn pneumatycznych, co pozwala na dostosowanie ich do specyficznych potrzeb produkcyjnych. Niemniej jednak istnieją również pewne ograniczenia związane z budową maszyn pneumatycznych. Wśród nich należy wymienić konieczność regularnej konserwacji oraz kontrolowania ciśnienia powietrza, co może generować dodatkowe koszty eksploatacyjne.
Jakie są kluczowe elementy budowy maszyn pneumatycznych
Aby maszyny pneumatyczne mogły działać efektywnie, konieczne jest zastosowanie odpowiednich elementów konstrukcyjnych, które zapewnią ich prawidłowe funkcjonowanie. Do kluczowych komponentów należą cylindry pneumatyczne, które odpowiadają za przekształcanie energii sprężonego powietrza w ruch mechaniczny. Cylindry te występują w różnych rozmiarach i typach, co pozwala na ich dostosowanie do konkretnych potrzeb aplikacyjnych. Kolejnym istotnym elementem są zawory sterujące, które regulują przepływ powietrza wewnątrz systemu oraz umożliwiają precyzyjne sterowanie ruchem cylindrów. Sprężarki to kolejny kluczowy komponent budowy maszyn pneumatycznych; odpowiadają one za generowanie sprężonego powietrza potrzebnego do działania całego układu. Ważne są także przewody oraz złączki, które łączą poszczególne elementy systemu i zapewniają szczelność układu.
Jakie są najnowsze trendy w budowie maszyn pneumatycznych
W ostatnich latach budowa maszyn pneumatycznych ewoluowała, a nowe technologie oraz innowacyjne rozwiązania zaczęły odgrywać coraz większą rolę w ich projektowaniu i wdrażaniu. Jednym z najważniejszych trendów jest automatyzacja procesów produkcyjnych, która pozwala na zwiększenie wydajności oraz redukcję kosztów operacyjnych. Wprowadzenie inteligentnych systemów sterowania umożliwia precyzyjne monitorowanie pracy maszyn pneumatycznych oraz dostosowywanie ich parametrów do zmieniających się warunków produkcji. Dzięki zastosowaniu czujników i systemów analitycznych możliwe jest zbieranie danych w czasie rzeczywistym, co pozwala na szybką reakcję na ewentualne problemy oraz optymalizację procesów. Kolejnym istotnym trendem jest rozwój materiałów i technologii produkcji komponentów pneumatycznych. Wykorzystanie nowoczesnych tworzyw sztucznych oraz lekkich stopów metali przyczynia się do zmniejszenia masy maszyn oraz poprawy ich efektywności energetycznej. Dodatkowo, rosnące zainteresowanie ekologicznymi rozwiązaniami sprawia, że producenci maszyn pneumatycznych poszukują sposobów na minimalizację zużycia energii oraz emisji hałasu.
Jakie są różnice między maszynami pneumatycznymi a hydraulicznymi
Maszyny pneumatyczne i hydrauliczne to dwa różne systemy napędowe, które mają swoje unikalne cechy i zastosowania. Główna różnica między nimi polega na medium roboczym; maszyny pneumatyczne wykorzystują sprężone powietrze, podczas gdy maszyny hydrauliczne działają na zasadzie cieczy hydraulicznej. Ta podstawowa różnica wpływa na wiele aspektów ich działania. Maszyny pneumatyczne są zazwyczaj lżejsze i bardziej kompaktowe niż hydrauliczne, co czyni je łatwiejszymi w instalacji i transportowaniu. Dodatkowo, systemy pneumatyczne charakteryzują się mniejszymi wymaganiami konserwacyjnymi, ponieważ nie ma ryzyka wycieków cieczy, co jest częstym problemem w systemach hydraulicznych. Z drugiej strony, maszyny hydrauliczne oferują znacznie większą siłę i moment obrotowy, co sprawia, że są bardziej odpowiednie do ciężkich prac przemysłowych wymagających dużej mocy. Warto również zauważyć, że maszyny hydrauliczne mogą działać w trudniejszych warunkach atmosferycznych oraz w aplikacjach wymagających precyzyjnego sterowania ruchem.
Jakie są kluczowe aspekty bezpieczeństwa przy budowie maszyn pneumatycznych
Bezpieczeństwo jest jednym z najważniejszych aspektów związanych z budową maszyn pneumatycznych. Właściwe zaprojektowanie systemu oraz jego komponentów ma kluczowe znaczenie dla zapewnienia bezpiecznej eksploatacji urządzeń. Przede wszystkim należy zwrócić uwagę na stosowanie odpowiednich materiałów oraz technologii produkcji, które będą odporne na wysokie ciśnienie sprężonego powietrza. Każdy element układu musi być starannie dobrany i przetestowany pod kątem wytrzymałości oraz szczelności, aby uniknąć ewentualnych awarii czy wycieków powietrza. Ważnym aspektem jest także regularne przeprowadzanie konserwacji i kontroli technicznych maszyn pneumatycznych, co pozwala na wczesne wykrycie ewentualnych usterek oraz zapobieganie niebezpiecznym sytuacjom. Należy również zadbać o odpowiednie szkolenie personelu obsługującego maszyny; pracownicy powinni być świadomi zasad bezpieczeństwa oraz procedur awaryjnych związanych z eksploatacją urządzeń pneumatycznych.
Jakie są koszty budowy i eksploatacji maszyn pneumatycznych
Koszty budowy i eksploatacji maszyn pneumatycznych mogą się znacznie różnić w zależności od wielu czynników, takich jak rodzaj zastosowanych komponentów, skomplikowanie konstrukcji czy specyfika aplikacji przemysłowej. Na etapie budowy kluczowe znaczenie ma dobór odpowiednich elementów, które będą spełniały wymagania dotyczące wydajności oraz niezawodności systemu. Wysokiej jakości komponenty mogą wiązać się z wyższymi kosztami początkowymi, ale często przekładają się na dłuższą żywotność oraz mniejsze wydatki związane z konserwacją i naprawami w przyszłości. Koszty eksploatacji obejmują przede wszystkim zużycie energii potrzebnej do generowania sprężonego powietrza oraz regularne serwisowanie urządzeń. Warto również uwzględnić koszty związane z ewentualnymi przestojami produkcyjnymi spowodowanymi awariami maszyn lub koniecznością przeprowadzania konserwacji.
Jakie są najczęstsze problemy związane z budową maszyn pneumatycznych
Budowa maszyn pneumatycznych może wiązać się z różnorodnymi problemami technicznymi oraz organizacyjnymi, które mogą wpłynąć na ich wydajność i niezawodność. Jednym z najczęstszych problemów jest niewłaściwy dobór komponentów do konkretnej aplikacji; użycie elementów o niewłaściwych parametrach może prowadzić do awarii lub obniżenia efektywności działania maszyny. Ponadto nieodpowiednia instalacja lub montaż poszczególnych elementów może skutkować nieszczelnościami układu czy problemami z przepływem powietrza. Kolejnym istotnym zagadnieniem jest konieczność regularnej konserwacji; zaniedbanie tego aspektu może prowadzić do szybszego zużycia komponentów oraz zwiększonego ryzyka awarii. Często występującym problemem są także błędy w programowaniu systemu sterującego; niewłaściwe ustawienia mogą prowadzić do nieefektywnego działania maszyny lub nawet jej uszkodzenia.